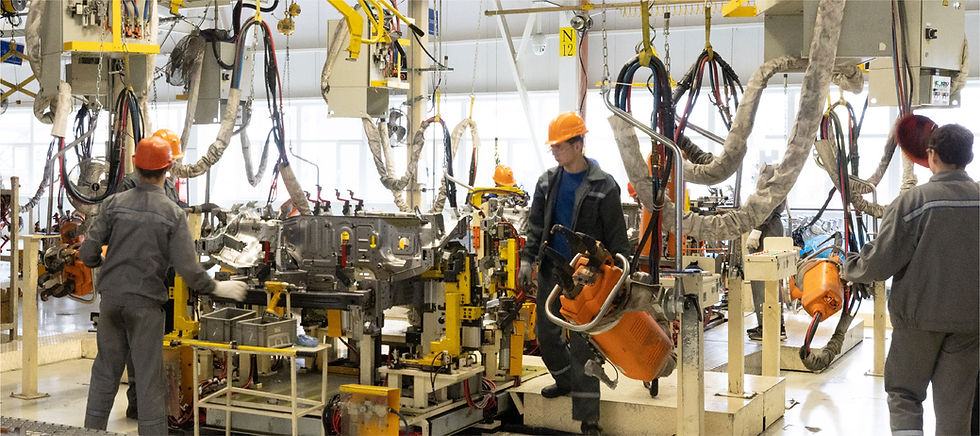
To kick things off in the discussion, let's ask:
What are the key components of a supply chain?
The key components of a supply chain include suppliers, manufacturers, distributors, retailers, and customers.
Let's Consider a Hypothetical Case Study: Canadian Automotive Parts Manufacturer
Canadian Manufacturing is a global company that produces and distributes automotive parts. Let's explore the key components of their supply chain:
01. Suppliers: Canadian Manufacturing works with a network of suppliers to source raw materials, components, and other inputs required for production. They establish strong relationships with reliable suppliers who provide high-quality materials at competitive prices.
Example: Canadian Manufacturing partners with a steel supplier to source the raw material needed for manufacturing automotive parts. They maintain open communication, negotiate contracts, and collaborate on quality control measures to ensure a steady supply of raw materials.
02. Procurement and Purchasing: Canadian Manufacturing employs effective procurement strategies to manage the purchasing of goods and services from suppliers. They engage in strategic sourcing, negotiate contracts, and implement efficient purchasing processes to optimize costs and ensure timely availability of materials.
Example: Canadian Manufacturing uses a centralized procurement system to streamline their purchasing processes. They leverage economies of scale by consolidating their purchasing power, negotiate favorable contracts with suppliers, and monitor supplier performance to maintain cost-efficiency.
03. Production: Canadian Manufacturing operates production facilities where raw materials and components are transformed into finished products. They employ efficient production processes, utilize technology and machinery, and ensure quality control measures to meet customer demands.
Example: Canadian Manufacturing uses automated assembly lines and quality control checkpoints to streamline their production processes. They implement lean manufacturing principles to minimize waste, optimize production cycles, and improve overall productivity.
04. Inventory Management: Canadian Manufacturing maintains an inventory of finished products, work-in-progress items, and raw materials to meet customer demand and minimize stockouts or excess inventory. They employ inventory management techniques to optimize inventory levels and reduce carrying costs.
Example: Canadian Manufacturing uses inventory management software to track inventory levels, monitor demand patterns, and automate reorder points. They implement a just-in-time (JIT) approach to reduce excess inventory and ensure timely replenishment of materials.
05. Warehousing and Distribution: Canadian Manufacturing operates warehouses and distribution centers to store, manage, and distribute their products. They employ effective logistics and transportation strategies to ensure timely and efficient delivery to customers.
Example: Canadian Manufacturing maintains regional distribution centers strategically located near their target markets. They collaborate with third-party logistics providers to optimize transportation routes, minimize delivery times, and manage warehousing operations.
06. Customer Service: Canadian Manufacturing focuses on providing excellent customer service to meet customer expectations and maintain strong relationships. They have dedicated customer service teams to handle inquiries, manage orders, and address any issues promptly.
Example: Canadian Manufacturing has a customer service hotline and online portal where customers can place orders, track shipments, and seek assistance. They prioritize responsiveness, provide timely updates, and address customer concerns promptly to enhance the overall customer experience.
Canadian Manufacturing's supply chain comprises key components such as suppliers, procurement, production, inventory management, warehousing and distribution, and customer service. By effectively managing these components, they ensure a reliable supply of materials, efficient production processes, optimized inventory levels, timely delivery, and excellent customer service, ultimately achieving customer satisfaction and business success.
Note: The above case study is purely hypothetical and does not represent any specific company or industry. It is provided for illustrative purposes to explain the concept of collaboration in the supply chain and its benefits.
Presented by
An initiative of VCARE Academy’s Education and Research Executive Board (EREB) and Education and Research Practitioners Board (ERPB)
If you have any questions or suggestions, please feel free to contact support operations at suppport@vcare.international and support@vcare.academy
Certification Programs
A successful career in supply chain necessitates a never-ending thirst for knowledge and the most up-to-date supply chain skills and knowledge. Even though continuing education and certification programs can take time and money, they help get your specialized knowledge or skills recognized.
Certified Stores and Stock Controller (CSSC)
Certified Production and Inventory Analyst (CPIA)
Mini Master and Master Classes
When professionals have training that other professionals lack, it distinguishes them and sets them apart from the crowd. Certification and master classes show that the professionals are committed to learning, excelling, and using best practices.
Supply Chain Framework and Strategy
Collaboration among Sustainability, Procurement and Supply Chain
Implementing 3PL and 4PL Strategies in the Value Chain
Supply Chain Sustainability with Circularity to Drive Profitability
Comments